En s’appuyant sur son expertise industrielle et ses marques historiques, le groupe Saint-Gobain a créé une Business Unit (BU) dédiée aux solutions modulaires et hors-site au sein de Saint-Gobain Solutions France, qui conçoit, produit et distribue des matériaux et services pour les marchés de l’habitat et de l’industrie. Objectif : accompagner l’ensemble de la chaîne de valeur – industriels, entreprises de construction, maîtres d’ouvrage et maîtres d’œuvre– dans la transformation du secteur en se positionnant en tant que fournisseur de solutions. Adrien Barbey, directeur de la BU Solutions Modulaires et Hors Site chez Saint-Gobain Solutions France, revient sur le rôle de cette BU dans la stratégie du groupe.
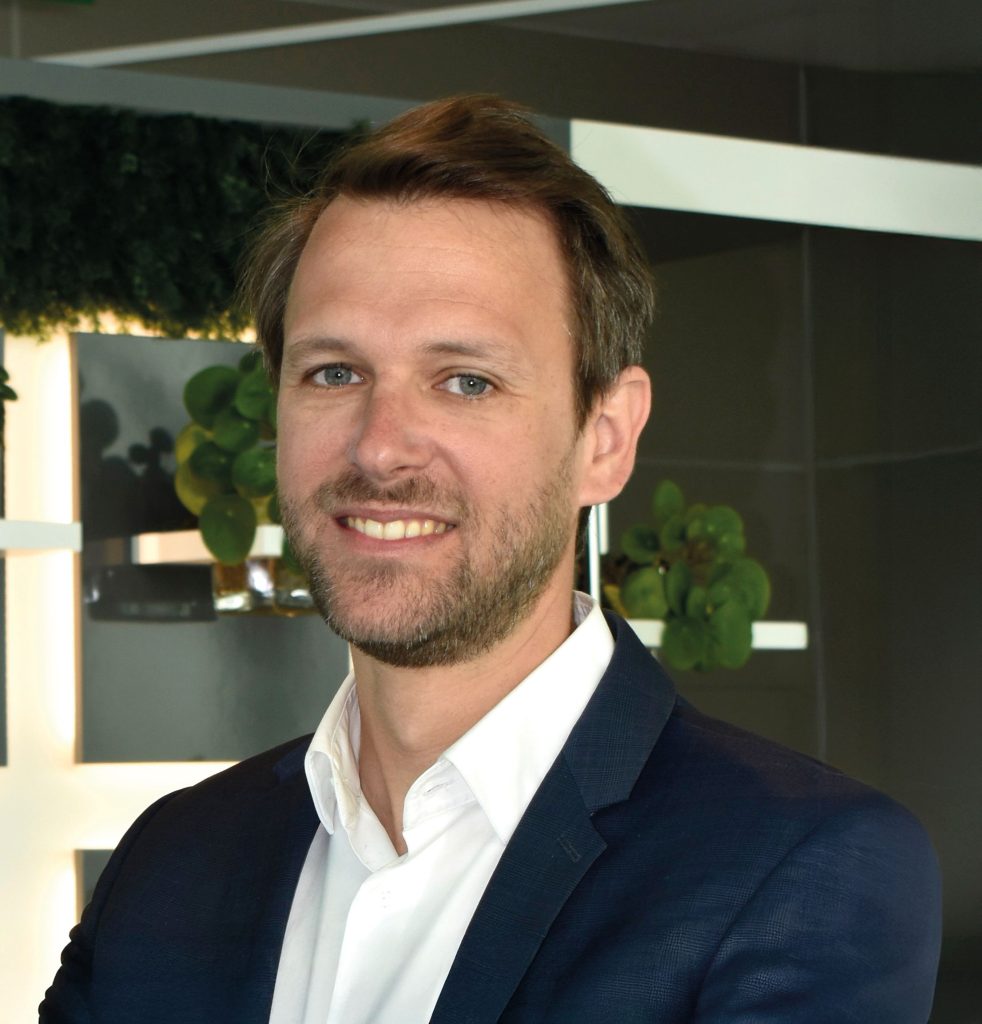
Adrien Barbey,
directeur de la BU Solutions Modulaires et Hors Site chez Saint-Gobain Solutions France
Quelle est la place de la construction hors-site dans la stratégie de Saint-Gobain ?
Adrien Barbey : La construction hors-site s’inscrit dans la stratégie globale du groupe de s’affirmer comme leader mondial de la construction durable. L’objectif est d’offrir des solutions bas carbone, performantes et compétitives qui facilitent l’adoption de ces nouveaux modes constructifs. Cela dit, elle tient une place particulière au sein du groupe, car elle se situe à l’intersection de plusieurs de nos activités. Saint-Gobain est structuré autour de deux approches : d’une part, les solutions pour la construction, notre cœur de métier le plus connu, et d’autre part, les industries de hautes performances, où nous jouons le rôle de fournisseur pour divers secteurs comme l’automobile ou l’électroménager. La construction hors-site est à l’intersection de ces deux univers. Ainsi, le groupe se positionne comme un équipementier pour les industriels de la construction.
En clair, vous n’êtes pas constructeur mais fournisseur de solutions ?
Exactement. Nous ne faisons pas d’assemblage, nous sommes avant tout un industriel des matériaux et un fournisseur de solutions complètes aux performances validées et certifiées, prêtes à assembler par nos clients. Nous comparons souvent notre activité à celle que nous avons dans l’industrie automobile, où nous codéveloppons des vitrages intelligents sans assembler les véhicules. Dans la construction hors-site, nous proposons des solutions destinées aux fabricants de modules 2D et 3D. Le large portefeuille d’activités du groupe permet de proposer des solutions allant de la structure légère (approvisionnement et taille du bois de charpente avec notre entité CIBM) à l’isolation multimatériaux (Isover) et la finition intérieure en voie sèche (Placo, Adfors, Ecophon, Clipso), en passant par les réseaux de second œuvre (pieuvres électriques et hydrauliques préfabriquées par notre entité Pro’fil).
Pourquoi avoir créé cette direction dédiée à la construction hors-site au sein du groupe ?
Cette direction a été mise en place pour structurer et renforcer notre offre dans ce domaine. Elle repose sur deux piliers : une approche commerciale grands comptes transverse permettant aux marques du groupe d’accéder à ce marché spécifique et un axe innovation et développement qui s’appuie sur l’expertise d’un bureau d’études dédié. Cette Business Unit (BU), bien que restreinte en taille, mobilise les expertises et fonctionne comme une organisation centrée sur les clients. Elle s’adresse notamment aux assembleurs industriels du hors-site, mais aussi à l’ensemble de la chaîne de valeur (entreprises générales, maîtres d’ouvrage, maîtrises d’œuvre, laboratoires, instituts de certification, etc.). Elle leur propose un réel partenariat de codéveloppement, à l’image de ce que nous avons fait avec Placo et Mathis pour la solution de plancher Azurtec-Placo. Mais notre offre s’est élargie au fil des ans. Cette direction a été placée sous l’entité Saint-Gobain Solutions France, qui travaillait déjà avec les grands comptes et les majors du bâtiment.
Vous parlez également d’une activité de prescription, en quoi consiste-t-elle ?
Elle consiste à dialoguer en amont avec les grandes maîtrises d’ouvrage publiques et privées ainsi que les majors du bâtiment afin d’accompagner les grands projets nationaux en prescrivant des solutions à forte valeur ajoutée. Elle préexistait à la création de la BU hors-site et visait principalement des modes constructifs traditionnels. À présent, elle permet d’identifier très tôt des projets qui se prêtent à la construction hors-site pour nous y associer et les accompagner tout au long de leur cycle de vie.
Sujet d’actualité : la réduction de l’empreinte carbone des bâtiments. En quoi la construction hors-site y contribue-t-elle ? Et comment travaillez-vous cet aspect en interne et en externe ?
Nous investissons considérablement dans la réduction de l’empreinte carbone. En interne, Saint-Gobain poursuit un objectif ambitieux de neutralité carbone d’ici 2050. Nous avons mis en place une feuille de route qui comprend la décarbonation de nos processus industriels (optimisation des usines, réduction des émissions directes), la réduction des émissions liées à la chaîne d’approvisionnement. En externe, notre objectif principal est avant tout d’aider nos clients à décarboner leurs propres activités par la promotion de solutions alternatives aux matériaux très émissifs. La construction hors-site joue un rôle majeur dans cette stratégie, car elle permet d’optimiser la consommation des ressources et de réduire l’impact carbone des bâtiments. Nous proposons des solutions légères et faiblement émissives en carbone, entièrement documentées sous l’aspect environnemental et sanitaire. L’ensemble de l’offre de matériaux est couvert par des FDES (Fiches de Déclaration Environnementale et Sanitaire) permettant aux clients de remplir leurs objectifs de certification environnementale. Nous nous alignons ainsi sur les exigences des industriels en termes de décarbonation et nous les accompagnons dans leurs feuilles de route environnementales.
« Nous nous alignons sur les exigences des industriels en termes de décarbonation et nous les accompagnons dans leurs feuilles de route environnementales. »
Quelle est votre valeur ajoutée pour accompagner cette transition vers la construction hors-site ?
Nous avons une équipe d’innovation avec un budget dédié qui poursuit deux axes. Le premier consiste à adapter nos solutions. Historiquement, nos produits sont conçus pour être mis en œuvre par des artisans. Dans le domaine du hors-site, ils sont repensés pour améliorer la productivité industrielle. Par exemple, nous avons développé des plaques agrafables ou clouables sur des tables d’industriels comme Glasroc X avec Placo pour répondre aux enjeux de la protection au feu extérieure des façades, ou Rigidur H. Cette dernière est une plaque de gypse-cellulose très robuste et dense offrant des performances de protection incendie, mais aussi thermiques, acoustiques et structurelles, adaptées à l’encapsulage des structures en bois, et ce dans des grands formats allant jusqu’à 2,5m x 6m. Nous proposons également des solutions de finition intérieure sèche: les plafonds en toile tendue Clipso, esthétiques et sans temps de séchage, facilitent l’intégration de systèmes d’éclairage, ou encore les toiles de verre Adfors peintes et prêtes à l’emploi. Ces solutions permettent d’économiser jusqu’à 30% des coûts fournis posés et de gagner jusqu’à neuf jours sur la mise en œuvre en usine. Pour un industriel, cela fait la différence en décuplant sa productivité, en réduisant les temps de cycle et donc en augmentant la capacité de production de ses usines. Le deuxième axe est l’optimisation technico-économique des modes constructifs. En nous appuyant sur des compétences de bureau d’études, nous effectuons des modélisations à l’échelle des bâtiments pour en optimiser les performances en termes d’empreinte carbone, de confort d’été ou encore d’acoustique afin de proposer à nos partenaires les complexes de parois les plus performants et compétitifs.
Quels sont les principaux défis ou freins à la construction sur la route du hors-site ?
L’adoption et la massification restent complexes en raison de plusieurs facteurs : d’une part l’équation économique par rapport à la construction traditionnelle doit s’améliorer. D’autre part, il y a des freins règlementaires et assurantiels à lever pour rassurer les maîtrises d’ouvrage et leurs assureurs. Sur ces deux thématiques, nous apportons un accompagnement solide et de réelles réponses à nos clients et à l’ensemble de la filière. Pour illustrer cette problématique, je peux vous citer un exemple : nous avons récemment accompagné le constructeur modulaire Vestack dans la conception de ses modules 3D sur un projet de résidence pour jeunes travailleurs afin de répondre aux contraintes acoustiques du labe lNF Habitat HQE. Nous avons conçu conjointement avec le BE acoustique Aida et Vestack différentes variantes possibles de complexes de plancher intégrant nos chapes sèches Rigidur Sol et nos suspentes acoustiques Intégra 2 Phonic. Nos acousticien sont validé leurs performances par essais in situ sur des modules prototypes. Le résultat : un complexe global de plafonds non seulement conformes aux exigences acoustiques mais aussi significativement réduit en poids, en coût et en temps d’assemblage. Le tout permet un coût fourni posé réduit de 30% par rapport à la conception initiale! La constitution de cette Business Unit reflète un réel engagement du groupe pour contribuer à lever ces freins et nos équipes font preuve d’une mobilisation sans faille.
Ce n’est un secret pour personne, le secteur de la construction est en crise. Est-ce un autre frein au développement du hors-site ?
Non, au contraire. Nous percevons la période actuelle comme une opportunité d’accélérer les efforts en R&D afin de renforcer la compétitivité de nos solutions avant une reprise du marché. L’industrialisation de la construction est plutôt vue comme un levier pour moderniser le secteur et offrir des solutions plus performantes et à meilleur coût.
Dans ce contexte, que mettez-vous en place pour accélérer le déploiement des solutions ?
Nous organisons des Tech Days deux fois par an pour réunir les industriels et les grands acteurs du secteur. Ces événements sont l’occasion d’aborder des thématiques clés comme la sécurité incendie, le confort d’été et les solutions de finition sèche. Ils permettent de présenter nos innovations et de créer un dialogue autour des enjeux de la construction industrialisée. C’est notre rôle d’équipementier de proposer une offre structurée et transverse, tout en accompagnant la transition écologique du secteur. Je l’ai déjà dit, mais j’insiste, l’industrialisation du bâtiment est un levier important pour moderniser la construction et répondre aux enjeux environnementaux, économiques et sociétaux.