Ce système combiné bois-béton offre tous les bénéfices de la construction hors-site : gain de temps, de ressources, de coûts et réduction des nuisances sur chantier. Tout en garantissant un bâtiment pérenne, à impact carbone fortement réduit et conforme à la RE2020.
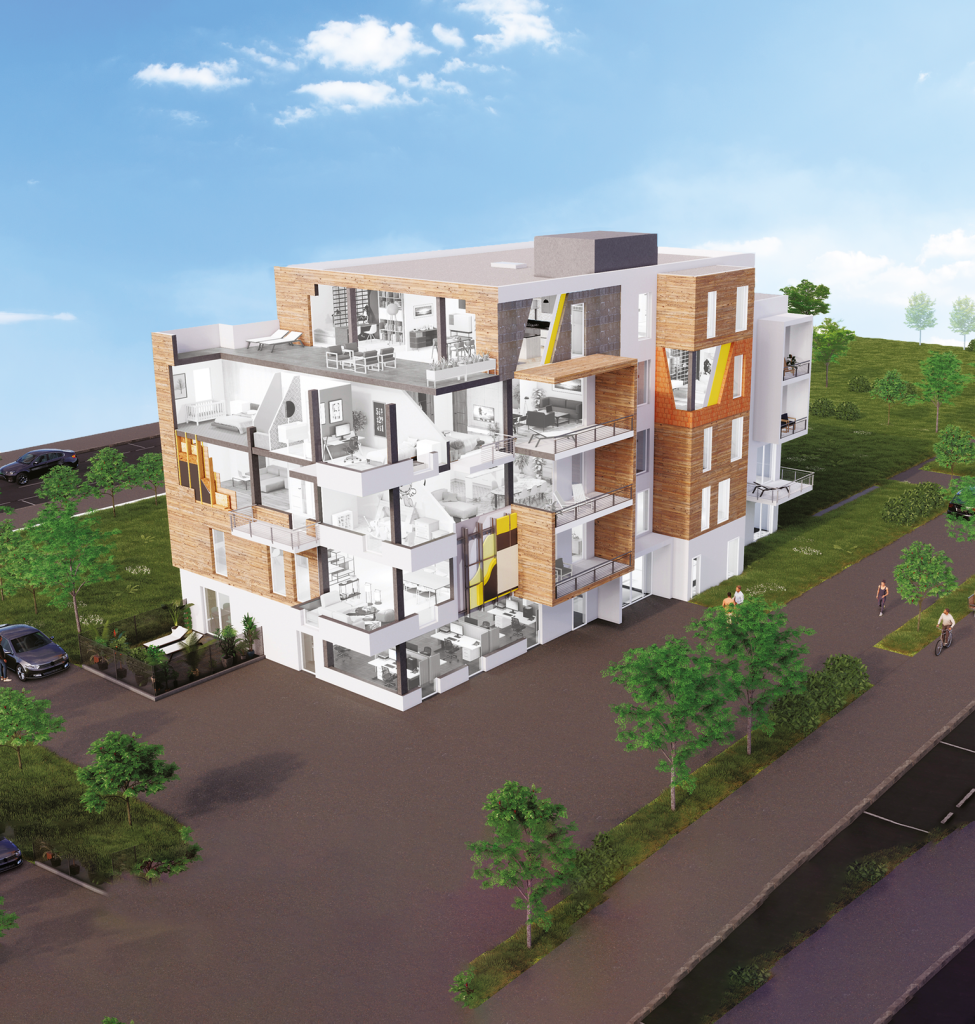
« Proposer des solutions de préfabrication industrielle bois et béton hors-site pour une décarbonation intelligente des bâtiments. » C’est ainsi que Rector, industriel de la préfabrication béton, et Techniwood, fabricant de façades préfabriquées en bois, ont présenté leur projet commun à Batimat, en octobre 2022. À savoir, un procédé constructif complet pour la réalisation de bâtiments dédiés au secteur tertiaire et aux logements collectifs. Cette solution technique associe le plancher-dalle préfabriqué sans mur porteur en béton bas carbone Caméléo de Rector et le panneau de façade Panobloc CLT à impact carbone négatif de Techniwood. Une proposition qui met en application ce qui est désormais un adage : le bon matériau au bon endroit.
Les deux industriels croient, en effet, en la complémentarité bois/béton: «La mixité, expliquait André de Chefdebien, directeur innovation et marketing stratégique chez Rector, lors d’une interview durant le Salon Batimat, est une façon de massifier la construction bas carbone. Sans elle, nous n’atteindrons pas les objectifs environnementaux à un coût économique raisonnable.» Et Dominique Pelissier, vice président de Techniwood, de poursuivre : « Avec les promoteurs, nous sommes confrontés à une logique économique assez dure. Si nous souhaitons développer la filière bois, nous devons avoir des coûts semblables à ceux du béton. D’où cette réflexion autour de la préfabrication et de l’optimisation, car nous raisonnons dans une logique de coût global. »
Cette approche 100 % hors-site et « bimisée » apporte aussi un maximum de flexibilité pour laisser libre cours à la créativité des architectes. « Il ne s’agit pas d’une structure poteaux-poutres, mais d’un système plancher-dalle soutenu par des poteaux libérant l’ensemble des plateaux de toute retombée. Ainsi ils sont reconfigurables à volonté pour de nouveaux usages », résume André de Chefdebien. En outre, cette transformation peut être anticipée en choisissant judicieusement l’emplacement des poteaux. Ce qui permet de minimiser les coûts et l’impact environnemental des reconversions. Autre intérêt du plancher-dalle : le confort acoustique apporté par la masse du matériau.
Reste à habiller cette structure. C’est là qu’interviennent les panneaux de façade développés par Techniwood. Fabriqués via un process industriel totalement automatisé, ces panneaux isolants sont composés d’un treillis structurel en bois. Soit un empilage de plis croisés, alternance de lames de bois massif et de bandes isolantes de remplissage. Fixés à la structure, livrés nus ou finis, ils constituent l’enveloppe du bâtiment et apportent les isolations thermique et acoustique. Techniquement, les deux industriels ont traité les problématiques de fixation et d’interfaces de façon à éviter toutes mauvaises surprises sur chantier. « D’où l’intérêt de se parler en amont, pour ne pas tomber dans des travers qui font que la solution ne serait pas économique », expliquent ils.